Chemical Industry Leader BASF Taps LSU to Help Optimize Its Operations Using AI
September 20, 2022
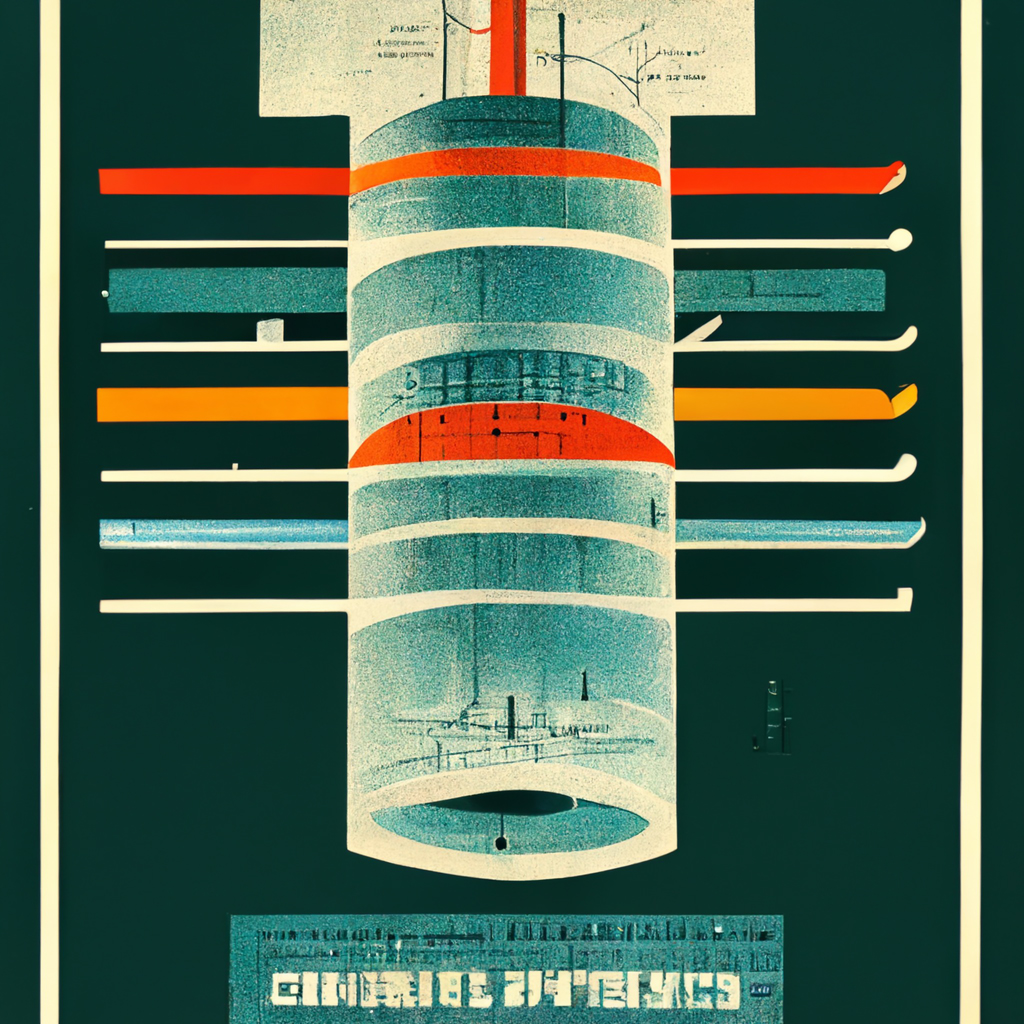
LSU researchers are using AI and machine learning to identify connections between continuously changing operating conditions at BASF’s Geismar chemical manufacturing plant and optimize production. BASF, the largest chemical producer in the world, has a longstanding partnership with LSU related to talent development, research and diversity and inclusion programs.
– Image generated by AI and featured in LSU’s fall 2022 issue of Working for Louisiana; the keywords were /imagine_chemical_tubes_pipelines_plant_interconnected.
BASF, the largest chemical producer in the world, is collaborating with LSU chemical engineers to better understand and predict its own production ebbs and flows using artificial intelligence, or AI. The project adds to an ongoing partnership between LSU and BASF to develop emerging STEM talent across disciplines in Louisiana.
BASF’s chemical manufacturing plant in Geismar, Louisiana is one of the company’s six largest integrated production sites across 80 countries. It supplies products to a wide variety of industries, including agriculture, construction, energy and health. Chemicals such as solvents, amines, resins, glues, electronic-grade chemicals, industrial gases, basic petrochemicals and inorganic chemicals are produced at Geismar in about 30 interconnected production units, each containing its own subunits.
“Chemical manufacturing is complex,” said Kerr Wall, digitalization manager in the monomers division at BASF. “Operating conditions can change minute to minute and there is a lot of data to mine. Big data gives a great opportunity to optimize our processes and become more predictive to improve our yields and our utility usage. This will make us more energy efficient and support our global value of producing chemicals for a sustainable future.”
BASF is working with LSU to develop better data mining processes to organize its data and more easily compare current operating conditions with historical data.
Wall and his colleague Eric Dixon, who is also in digitalization and has been a production engineer in the BASF intermediates division since he graduated from LSU in 2008, had read about the research done by LSU Professor José Romagnoli on optimization and control of complex systems, especially using AI and machine learning to derive new knowledge from heterogenous data.
“It just made perfect sense for us to collaborate with LSU...José [Romagnoli] has more than 500 publications and a lifetime of experience with process control, machine learning and other areas that would be beneficial for us to understand. We are trying to automatically determine the most important process and quality parameters to help us link current data to historical data and then use this data as predictive tools to enable process optimization.”
Kerr Wall, BASF digitalization manager in the monomers division
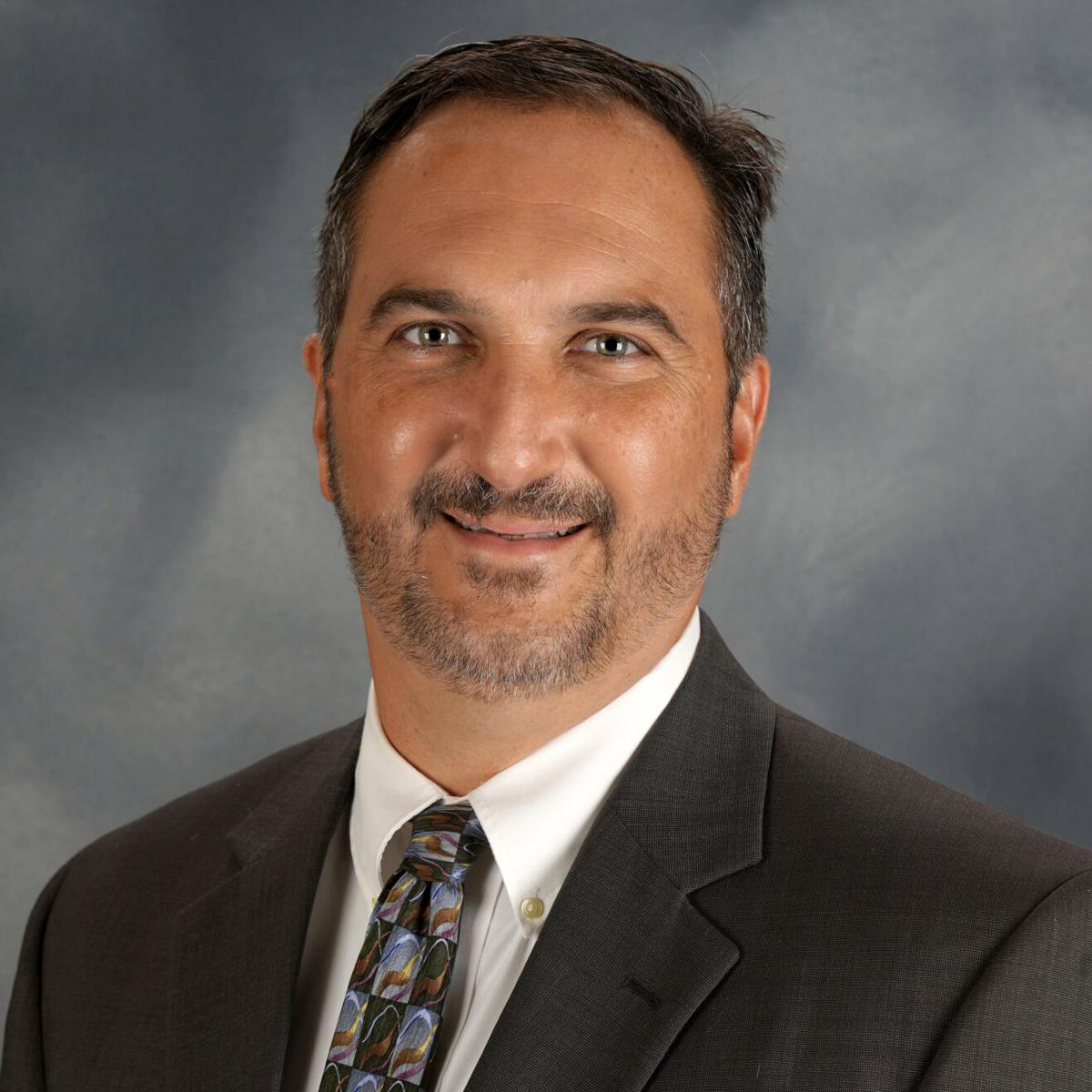
Kerr Wall, an LSU chemical engineering graduate (’99), is the digitalization manager of BASF’s Geismar monomers division. He appreciates the power of AI and machine learning to create “soft sensors”—entirely data-driven estimates—in places where physical sensors are impractical or impossible, such as in chemical manufacturing plants.
Part of the goal of the project is to come up with optimized and automated workflows, and develop something called soft sensors, a machine learning term often used in manufacturing.
“Soft sensors are when the data alone can tell you the real-time quality parameters of your material, for example, without you having to run lab samples throughout the day,” Wall said. “Soft sensors help estimate a particular variable—at any given moment. This can also help predict the ultimate quality of what we produce.”
Physical sensors are often impractical or impossible to use in the extreme operating conditions of a chemical manufacturing plant.
“Instead of waiting 12 hours for a lab sample or for the next shift to take a new sample, LSU can help us find a way to predict what is happening inside our units, just based on data and AI,” Wall said.
The LSU researchers are using an unsupervised clustering approach to assist BASF in categorizing and labeling their production data. Time is a key parameter, since a major goal of the project is to discover how a change in one production unit might force different operating conditions in other, connected units.
“We can use flow rate; the material that’s coming in and out of a plant,” Dixon said. “If one plant is running at 50 percent capacity and a sister plant shuts down, the feeding plant might need to reduce rates by 20 percent until everything is worked out. Understanding how and when one event leads to another makes it possible for us to make better decisions as events occur and evolve.”
“Unsupervised machine learning allows us to capture the intrinsic behavior of processes and discover things we weren’t necessarily even looking for,” said LSU Cain Endowed Chair & Professor of Chemical Engineering José Romagnoli. “With machine learning and AI, we have a better opportunity to optimize production.”
His colleague, LSU Cain Department of Chemical Engineering Assistant Professor Xun Tang, is also involved in the project.
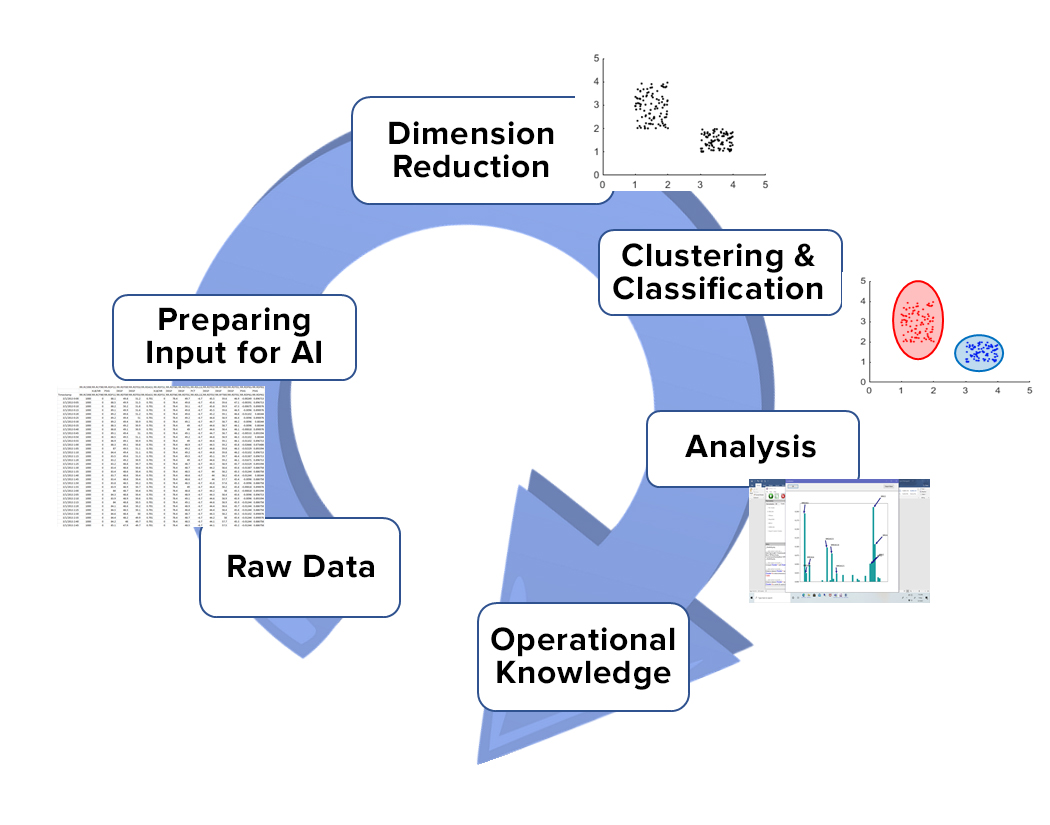
An unsupervised learning approach allows LSU’s machine learning to “think out of the box” and discover production patterns and correlations neither BASF nor LSU chemical engineers might think to look for. Knowing how a change in one unit might force a change in other, connected units helps optimize operations in large and integrated plants, such as BASF’s plant in Geismar, south of Baton Rouge.
“BASF has a lot of production data, but it can be a challenge to understand the underlying dynamics,” Tang said. “Through this collaborative project, we can learn directly from the data in order to identify patterns. Then we can use what we learned to predict new conditions to optimize and maintain the operation of the system. This way, we can help BASF automate and optimize their plant, and also improve the yield and quality of their product while reducing costs.”
Prior to this collaboration with BASF, Romagnoli and his team did a similar project with the oil and gas company ExxonMobil. The first LSU student to graduate with a PhD who had worked on that project is Gregory Robertson, who now leads application engineers in the Automation and Innovation section of ExxonMobil in Baton Rouge.
“It takes a non-trivial amount of knowledge to develop data-driven techniques for fault detection and diagnosis,” Robertson said. “In most cases, you have sensors on key variables to protect from abnormal events. But when a faulty condition is difficult to define, the data-driven techniques LSU is developing are a useful tool in your toolkit.”
BASF’s longstanding partnership with LSU encompasses a multitude of areas, including career and recruiting programs for students (scholarships, internships, mentoring, job shadowing, senior projects, etc.), sustainability efforts across campus, including the BASF Sustainable Living Lab, research collaboration, diversity and inclusion programs in STEM fields to engage women, minorities and veterans, and more.
Kerr Wall and Eric Dixon are both long-time LSU chemical engineering graduates (1999 and 2008, respectively). Wall is also a current visiting professor at LSU. He holds a PhD in bioinformatics and is currently conducting research on aging with Assistant Professor Alyssa Johnson in the LSU Department of Biological Sciences.